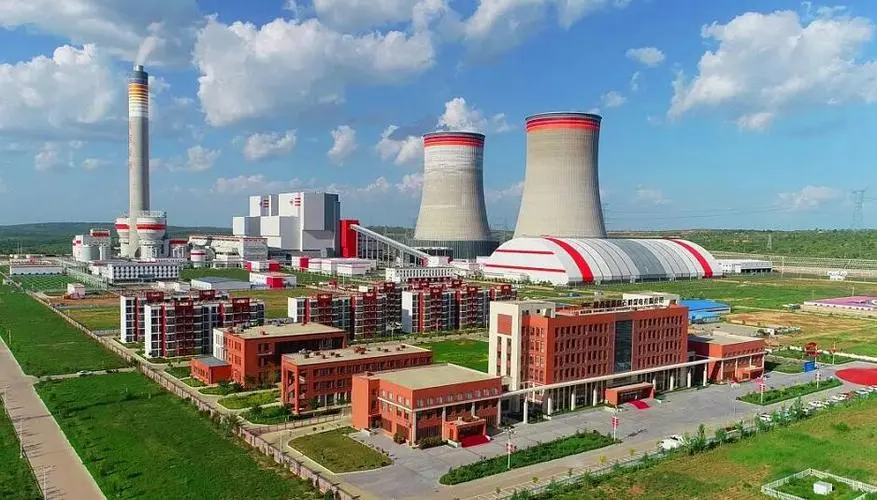
If you are interested in cooperation, please contact us immediately, we will give you feedback as soon as possible!
Whatsapp : +8613176258356
Email : [email protected]
Items | Details |
---|---|
Product Name | Color Coated Coil |
Place of Origin | Jiangsu, China |
Production Process | Using hot – dip galvanized sheets, hot – dip aluminum – zinc sheets, or electrogalvanized sheets as the base material. First, surface pretreatment is carried out, including chemical degreasing and chemical conversion treatment to remove oil, dirt, and impurities and form a conversion film to enhance the adhesion of the coating. Then, one or more layers of organic coatings are applied by roll coating, and finally, cured by high – temperature baking. |
Execution Standards | Comply with domestic standards such as GB/T 12754 – 2019 Colored Coated Steel Sheets and Strips; internationally, refer to relevant ASTM standards (such as ASTM A755, etc.). |
Base Materials | Hot – dip galvanized base materials (such as DX51D + Z, etc.), hot – dip aluminum – zinc base materials (such as AZ150, etc.), electrogalvanized base materials (such as DC01 + ZE, etc.). |
Coating Types | Polyester (PE): Rich in colors, with good adhesion and low cost, suitable for general construction and home appliance fields. Silicone – modified polyester (SMP): Higher hardness, wear resistance, and heat resistance, with better durability than PE, used for buildings and industrial applications with higher performance requirements. High – durability polyester (HDP): Outstanding UV resistance and weather resistance, often used in outdoor buildings. Polyvinylidene fluoride (PVDF): Excellent weather resistance, chemical corrosion resistance, and anti – chalking properties, suitable for high – end buildings and harsh environments, with a relatively high cost. |
Coating Structures | 2/1: Coated twice on the upper surface and once on the lower surface, baked twice, suitable for sandwich panels. 2/1m: Coated twice on both the upper and lower surfaces, baked once, used for single – layer profiled sheets and sandwich panels. 2/2: Coated twice on both the upper and lower surfaces, baked twice, mostly used for single – layer profiled sheets. |
Thickness | 0.15mm – 2.0mm (adjustable according to production capacity) |
Width | 600mm – 1500mm |
Inner Diameter of Coil | 508mm / 610mm (common specifications, customizable) |
Coil Weight | 3 – 8 tons (adjustable according to requirements) |
Colors | Conventional colors such as off – white, ocean blue, brick red, etc. Special colors can be customized according to the Pantone color card. |
Corrosion Resistance | In addition to the protection of the base material itself, the organic coating isolates air, moisture, and chemical substances, extending the service life. The outdoor service life of color – coated coils with hot – dip galvanized base materials can reach 10 – 30 years. |
Decorativeness | Rich in colors, with a smooth surface, which can enhance the aesthetics of buildings and products. |
Workability | Good bending, stamping, and shearing properties to meet diverse processing requirements. |
Durability | Different coatings ensure different years of weather resistance and anti – aging performance. For example, PVDF – coated coils can last for more than 20 years. |
Construction Industry | Roofs, walls, ceilings, rolling shutters, light – gauge steel keels, etc., providing protection and decoration for buildings. |
Home Appliance Manufacturing | Shells and internal decorative parts of refrigerators, air conditioners, washing machines, microwave ovens, etc. |
Furniture Manufacturing | Panels and frames of cabinets, wardrobes, office furniture, etc. |
Transportation | Exterior decoration and protection of car bodies, train carriages, containers, etc. |
Others | Billboards, display racks, ventilation ducts, prefabricated houses, etc. |
Quality Assurance | Provide material certificates, coating performance inspection reports, and support third – party inspection. |
Packaging Methods | Moisture – proof paper + steel strip bundling, or wooden box packaging to prevent scratches, color fading, and moisture during transportation. |
Delivery Time | 3 – 7 days for regular orders; 10 – 20 days for customized orders. |
Payment Terms | T/T (Telegraphic Transfer), L/C (Letter of Credit), etc., negotiable. |
After – sales Service | Provide technical support. In case of quality problems, negotiate returns and exchanges. |
The surface is flat and smooth, with rich and varied colors, good gloss and decorativeness, and various colors and textures can be provided according to needs.
It varies depending on the substrate and coating materials used, but is generally similar to the density of the metal substrate used (such as galvanized sheet, galvanized sheet, etc.), usually around 7.8-7.9g/cm³.
The presence of the coating makes the surface hardness of the color-coated coil higher than that of ordinary metal sheets. Different types of coatings have different hardnesses. For example, polyvinylidene fluoride (PVDF) coatings have a higher hardness and can effectively resist scratches and wear.
It has a certain degree of flexibility and can be bent, stamped, and processed without cracking or shedding the coating. This makes it suitable for molding of various shapes, such as making roof panels and wall panels for construction.
The thermal conductivity is relatively low and has certain thermal insulation properties. In a high temperature environment, it can prevent the rapid transfer of heat to a certain extent, which helps to save energy in buildings. At the same time, different coatings have different heat resistance, such as the heat resistance of silicon-modified polyester (SMP) coating is better than that of ordinary polyester (PE) coating.
This is one of the important chemical properties of color-coated coils. The substrate is usually galvanized or galvanized, which has a certain corrosion resistance, and the coating further isolates the metal substrate from the corrosive substances such as air, moisture, acid and alkali in the outside world, greatly improving the overall corrosion resistance. For example, in outdoor environments, color-coated coils can be used for many years without obvious rust.
The coating of color-coated coils has good weather resistance and can resist the erosion of natural factors such as ultraviolet rays, rain, wind and sand, and is not prone to fading, powdering, etc. Color-coated coils like polyvinylidene fluoride (PVDF) coatings can still maintain good color and performance under long-term outdoor exposure, and the service life can reach more than 20 years.
In general use environments, the coating of color-coated coils is chemically stable and not easy to react chemically with common chemicals. However, in the case of long-term contact with corrosive chemicals such as strong acids and alkalis, the coating may be damaged, thus affecting its protective performance.
Color-coated coils with different types of coatings have different flammability. Generally speaking, color-coated coils with ordinary polyester coatings are flame-retardant materials. When encountering open flames, they will burn to a certain extent, but the burning speed is slow, and they will extinguish themselves after leaving the fire source. Some special fire-retardant coating color-coated coils have better flame retardant properties and can effectively delay the spread of fire.
Color coated coil is widely used in various fields. It is used for roofs and walls in buildings, which are both protective and beautiful; it is used as refrigerator and air conditioner shells in the home appliance field to improve the texture; it is used for cabinets and wardrobe panels in furniture manufacturing; it is used to cover the surface of automobile bodies and containers in the transportation industry; it is also used for billboards, ventilation ducts, etc., with its colorful appearance and corrosion resistance, it can meet diverse needs.
Jiangsu Rongyi Metal Co., Ltd. is a professional metal products supplier based in Wuxi, Jiangsu Province, China.